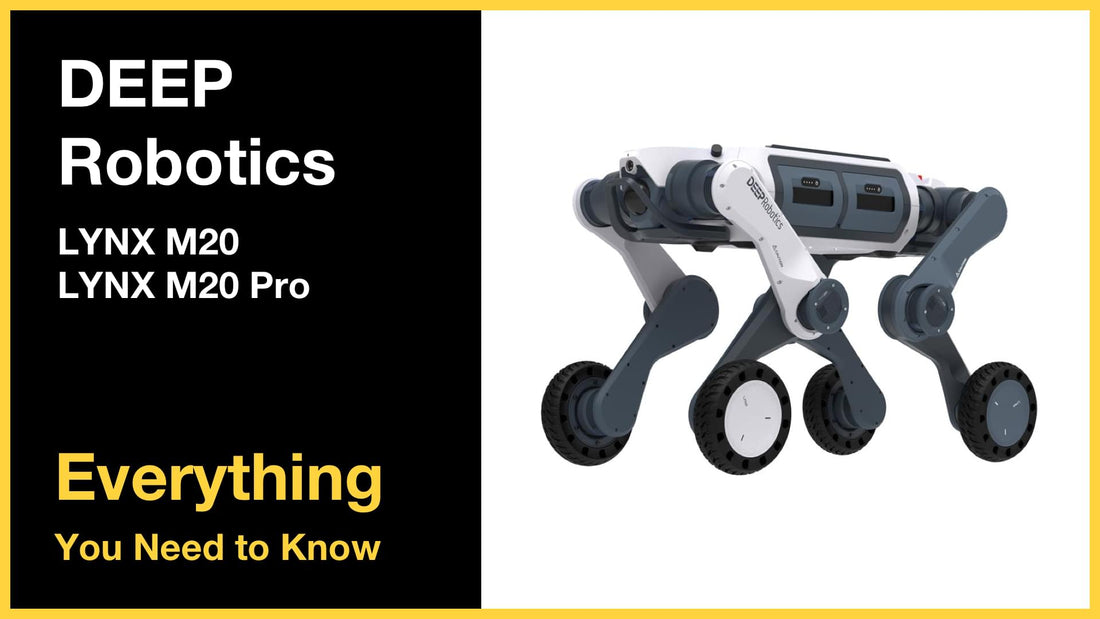
DEEP Robotics LYNX M20 series - Everything You Need to Know
BIKMAN TECHWelcome to BIKMAN TECH, where we explore the cutting edge of technological innovation. In this comprehensive review, we delve into the groundbreaking DEEP Robotics LYNX M20 series, a revolutionary wheeled-legged robot poised to redefine industrial automation. Discover how this advanced platform is meticulously engineered to tackle the most challenging jobs, from navigating hazardous environments for material handling to conducting all-terrain infrastructure inspections. Join us as we unpack the sophisticated design, pioneering technology, and impressive performance that distinguish the LYNX M20 as a true leader in the next generation of robotic solutions.
1. Introduction: DEEP Robotics and LYNX M20
The company DEEP Robotics specializes in embodied AI technology, focusing on the development and application of autonomous quadruped robots. They claim they are the first company in China to achieve fully autonomous substation inspections using these robots. Its technology is used in various industries, including power station and factory inspections, tunnel exploration, emergency rescue, fire detection, and scientific research. DEEP Robotics has participated in projects like the Singapore National Grid and disaster relief drills.
1.1. What Exactly is the DEEP Robotics LYNX M20?
The DEEP Robotics LYNX M20 series is an industry-grade, mid-sized wheeled-legged robot meticulously engineered by DEEP Robotics. Its standout characteristic is a unique hybrid locomotion system, ingeniously combining the speed of wheels with the unmatched agility of legs. This makes it, as DEEP Robotics claims, the "world's first mid-sized wheeled-legged robot built specifically for challenging terrains and hazardous environments during industrial operation". For those familiar with DEEP Robotics' origins, its Chinese name is 云深处科技 山猫M20 系列 (Yún Shēn Chù Kējì Shānmāo M20).
The "wheeled-legged" design isn't merely an added feature; it's a strategic engineering response to the inherent limitations often faced by purely wheeled or purely legged robots in diverse and demanding industrial settings. Wheeled robots, while fast on smooth surfaces, typically struggle with significant obstacles or very rough terrain. Conversely, legged robots excel in navigating complex landscapes but are often slower and consume more power on flat ground. The LYNX M20 is designed to "fuse wheeled speed with legged agility", allowing it to "zip along on four wheels when speed is of the essence, and independently lock them for walking mode" when the terrain calls for it. This hybrid approach optimizes both speed and terrain navigation by seamlessly switching modes, offering a versatile solution for multifaceted missions. This adaptability dramatically expands its operational envelope, making it suitable for tasks that involve traversing mixed environments—such as moving from a factory floor to an outdoor rubble field—without the need for multiple specialized robots.
1.2. Designed for the Toughest Jobs: Who is the LYNX M20 For?
The LYNX M20 series is engineered for industries and professionals who require robust robotic solutions for operations in hazardous settings, extreme environments, and across challenging terrains. Its applications are vast and varied, including:
- Power line and infrastructure inspection: Enhancing safety and efficiency in maintaining critical infrastructure.
- Emergency response, such as firefighting support, disaster relief, and locating survivors in collapsed structures: Providing crucial assistance in high-stakes situations.
- Logistics and distribution in difficult-to-access areas: Ensuring supplies and materials reach their destination, no matter the obstacle.
- Scientific exploration in remote or inhospitable locations: Pushing the boundaries of research in environments unsafe for humans.
- Surveying power plants, pipelines, and construction sites: Offering detailed and accurate data collection for large-scale projects.
- Operations in the mining sector and handling of hazardous materials: Improving safety and productivity in demanding mining operations.
Essentially, the LYNX M20 aims to bridge the operational gap between manual human labor and heavy machinery, especially in areas that are too dangerous, confined, or complex for traditional approaches. The wide array of potential applications strongly suggests that DEEP Robotics has developed a versatile platform solution. With a significant payload capacity and modular expansion capabilities, the LYNX M20 can be adapted with different sensors and tools for various industries, rather than being a single-purpose machine. This points towards a future where the base unit can be customized by end-users or integrators, fostering an ecosystem of specialized accessories and payloads for this advanced industrial robot.
2. Built to Endure: Design, Build Quality, and Portability of the LYNX M20 🛡️
2.1. Rugged Engineering: The LYNX M20's Chassis and IP66 Rating
The LYNX M20 boasts an industrial-grade build quality, meticulously designed for exceptional durability in the field. A key testament to its ruggedness is its IP66 rating. This certification signifies that the robot is completely dust-tight and protected against powerful water jets, making it highly suitable for operation during rainstorms and even in shallow water. Adding to its resilience, the LYNX M20 can operate effectively across a wide temperature range, from a frigid -20°C to a scorching 55°C (that's -4°F to 131°F), underscoring its readiness for extreme environmental conditions. It's worth noting that while some older or more general "Lynx" robot documentation might mention an IP54 rating, sources specific to the M20 series consistently confirm the higher IP66 protection level, crucial for any all-terrain robot.
This high level of environmental protection—IP66 and broad temperature tolerance—isn't just a specification; it's a critical enabler for new operational paradigms. It allows for continuous or on-demand deployment in conditions that would typically halt less protected equipment or pose significant risks to human workers. Many industrial sites, such as mines, construction zones, and chemical plants, as well as disaster areas, inherently involve exposure to dust, water, and temperature extremes. The LYNX M20's robust protection translates directly into increased operational availability and a reduced risk of mission failure due to environmental factors. This empowers industries to consider robotic deployment in scenarios previously deemed too hostile for automation, potentially facilitating 24/7 operations regardless of weather, thereby enhancing both efficiency and safety with this wheeled-legged robot.
2.2. The Best of Both Worlds: Innovative Wheeled-Legged Design of the LYNX M20
The core of the LYNX M20's adaptability lies in its innovative hybrid wheeled-legged design. This system masterfully combines the speed and efficiency of wheels on flat or semi-even surfaces with the superior agility and obstacle-negotiating capabilities of legs when faced with complex, uneven terrain. The robot features hyper-flexible joints and the ability to seamlessly switch between leg-wheel modes and configurations, such as "front-elbow/rear-knee" patterns. These configurations are not arbitrary; they provide distinct advantages. For instance, the "front-elbow, rear-knee" mode, with reversely bent hind legs, allows the robot to navigate through tight corners and confined spaces with remarkable ease. When encountering obstacles or needing to walk, the wheels can lock, transforming into stable feet for clambering or careful stepping, a key feature for any industrial robot designed for varied environments.
This sophisticated approach to locomotion, particularly the "hyper-flexible joints" and multiple leg configurations like "front-elbow/rear-knee" and "full-elbow" mode (used for climbing stairs), is indicative of advanced bio-inspired robotics. It moves beyond simple quadrupedal walking to emulate a broader range of animalistic movements. This kinematic complexity suggests highly advanced motion planning algorithms and control systems are at play, allowing the DEEP Robotics LYNX M20 to intelligently adapt its physical form and movement strategy to the immediate environmental challenges, rather than being constrained by a single mode of locomotion. This is particularly beneficial in unstructured and unpredictable environments, such as those found at disaster sites or active construction zones.
2.3. Compact Footprint, Big Capabilities: LYNX M20 Dimensions and Weight
Despite its robust capabilities, the LYNX M20 maintains a relatively compact and manageable profile. Its standing dimensions are 820mm in length, 430mm in width, and 570mm in height (approximately 32.3 inches x 16.9 inches x 22.4 inches). Including its battery, the robot weighs 33 kg (approximately 72.8 lbs). This manageable weight is a significant practical advantage, as it allows the LYNX M20 to be transported and deployed by a single operator. This ease of deployment is crucial for rapid response scenarios or operations in remote locations where heavy lifting equipment may not be available for such an advanced wheeled-legged robot.
Furthermore, its design allows it to navigate through narrow spaces, requiring a clearance of just 50 cm (approximately 19.7 inches). This ability to traverse tight corridors, tunnels, or cluttered industrial environments further enhances its operational versatility. The careful balance struck between a relatively lightweight, single-operator portable design and its substantial payload capacity (15 kg effective, 50 kg maximum) alongside advanced sensory and mobility features, points to a high degree of engineering optimization focused on real-world field utility. Achieving this power-to-weight and feature-to-weight ratio means the LYNX M20 is not only capable but also practical to deploy and redeploy quickly, offering a significant logistical advantage for various robotic solutions.
3. Decoding the Technology: Key Features of the LYNX M20 Series 💡
3.1. Go Anywhere, Do Anything: All-Terrain Mastery of the LYNX M20
The LYNX M20 is engineered to live up to its "all-terrain" promise. It's built to conquer a remarkable variety of challenging surfaces, including rugged mountain trails, muddy wetlands, debris-strewn ruins, desert sands, stepped inclines, and even unstable bridges. This isn't just about raw power; the robot autonomously perceives the terrain and intelligently adjusts its gait and posture to match. This adaptive capability is powered by advanced AI motion control algorithms and, significantly, reinforcement learning, making the LYNX M20 a truly intelligent all-terrain robot.
The incorporation of reinforcement learning is particularly noteworthy. It suggests that the LYNX M20's capabilities are not static; rather, they can evolve and improve over time. This could occur through collective learning across a fleet of robots or through specific training regimens for new, unforeseen environments or tasks. This type of machine learning, where an agent learns by trial and error, receiving feedback for its actions, implies the robot isn't solely reliant on pre-programmed responses for every conceivable terrain. This opens the door to enhanced autonomy and robustness, especially in truly novel or rapidly changing environments. It suggests a future where these DEEP Robotics platforms become increasingly adept and efficient in their specific operational contexts as they accumulate more "experience," potentially reducing the need for constant manual reprogramming when faced with new challenges.
3.2. Seeing is Believing: Advanced LiDAR and Vision Systems in the LYNX M20
To navigate and understand its complex surroundings, the LYNX M20 is equipped with a sophisticated sensor suite. Central to this are dual 96-line LiDAR systems. These provide a comprehensive 360° horizontal by 90° vertical Field of View (FOV), generating a dense point cloud (approximately 860,000 points per second from each LiDAR) crucial for real-time mapping, precise navigation, and robust omnidirectional obstacle avoidance. The choice of dual LiDARs, as specified on the manufacturer's official site, over a single unit mentioned in some third-party reports, significantly enhances perceptual redundancy. This dual setup offers overlapping fields of view and data from different perspectives, which is critical for reliable autonomous navigation in complex, cluttered, and dynamic environments where sensor occlusion or partial failure can be major issues. It allows for a more complete and accurate 3D environmental model, improving obstacle detection, path planning, and offering a degree of fault tolerance for this advanced industrial robot. This is a more costly but ultimately more robust solution for high-reliability operations.
Complementing the LiDAR are dual wide-angle cameras that provide live video feeds and capture visual data for operators or further processing. To ensure operational capability in all lighting conditions, the LYNX M20 also features front and rear bidirectional lighting, enabling it to navigate and perform tasks even in complete darkness or dimly lit environments, a critical feature for operations in hazardous environments.
3.3. Smart Moves: Intelligent Navigation and Autonomous Operation of the LYNX M20
The LYNX M20 series is designed for intelligent operation. Key features underpinning its autonomy include omnidirectional obstacle avoidance, allowing it to detect and navigate around impediments from any direction. It utilizes a point cloud surround view, generated by its LiDAR systems, to build a comprehensive understanding of its immediate environment. For remote operations, RF image transmission provides a reliable link for video feeds. Furthermore, the platform supports OTA (Over-The-Air) upgrades, enabling software enhancements and new features to be deployed remotely, ensuring the robot's capabilities can evolve over time. These features solidify the LYNX M20's position as a top-tier wheeled-legged robot.
The LYNX M20 Pro version takes autonomy a step further by incorporating SLAM (Simultaneous Localization and Mapping)-based positioning and mapping and full autonomous navigation features as standard. This distinction between the M20 and M20 Pro suggests a tiered product strategy. Users who primarily need teleoperation with robust obstacle avoidance might find the standard M20 sufficient, while those requiring the robot to perform complex missions independently in unknown or dynamic environments (like long-duration patrols or mapping large, uncharted areas) would necessitate the advanced capabilities of the M20 Pro. This tiered approach allows DEEP Robotics to cater to a broader spectrum of user needs for their robotic solutions and potential investment levels.
3.4. Powering Through: Hot-Swappable Batteries and Endurance of the LYNX M20
Continuous operation in the field is a critical requirement for industrial robots, and the LYNX M20 addresses this with a hot-swappable battery design. This allows batteries to be exchanged quickly without shutting down the robot, enabling extended missions and minimizing downtime. The system is often referred to as a dual battery system in broader "Lynx" contexts, and the M20 specifically benefits from this quick-swap capability, crucial for demanding industrial robot applications.
This hot-swappable battery feature, combined with a relatively quick charging time of just 1.5 hours per single battery, fundamentally changes the operational calculus for long-duration missions. It enables near-continuous operation with a modest pool of batteries. For example, with two batteries, one can be charging while the other powers the robot. Given the 2.5-hour loaded runtime, a freshly charged battery would be ready well before the active one is depleted. This effectively addresses one of the major limitations of battery-powered field robots: endurance. For tasks like continuous surveillance, extensive site inspections, or maintaining a persistent presence in an emergency zone, the hot-swappable battery system makes the DEEP Robotics LYNX M20 a far more practical and reliable tool, capable of operating for durations comparable to, or even exceeding, human work shifts.
3.5. Heavy Lifting: LYNX M20 Payload Capacity and Versatility
The LYNX M20 series is not just about mobility; it's also designed to carry essential equipment. It boasts an effective payload capacity of 15 kg (approximately 33 lbs) and a significantly higher maximum load capacity of 50 kg (approximately 110 lbs). This capacity allows for the mounting of a wide variety of sensors, tools, or supplies, tailoring the robot to specific mission requirements. To facilitate this, the robot is engineered with modular expansion capabilities and features a range of expansion ports and mounting interfaces. This high payload capacity enhances its utility as a versatile industrial robot.
The distinction between "effective payload" (15 kg) and "maximum load capacity" (50 kg) is important for users to understand. The 15 kg effective payload is likely the weight the robot can carry while maintaining its full dynamic performance, agility, and stated endurance figures (which are specified with a 15 kg load). The 50 kg maximum load capacity might be intended for more static carrying tasks or slower, less dynamic movements where peak agility is not the primary concern. This offers flexibility but requires careful consideration during payload design and mission planning to ensure optimal performance and avoid overburdening the system, which could impact speed, maneuverability, and battery life of the LYNX M20.
4. Performance Unleashed: Speed, Agility, and Obstacle Negotiation of the LYNX M20 🚀
4.1. Swift and Sure-Footed: Real-World Speed and Maneuverability of the LYNX M20
The LYNX M20 demonstrates impressive agility. Its operating maximum speed is 2 meters per second (m/s), which translates to approximately 7.2 kilometers per hour (km/h) or 4.5 miles per hour (mph). This is the practical speed users can expect for many autonomous or teleoperated tasks. However, the platform has a higher lab-tested maximum speed of 5 m/s (approximately 18 km/h or 11.2 mph). The manufacturer notes that this peak speed is safety-limited to 3 m/s in standard user mode, and some sources specify the 18 km/h figure particularly for its wheeled mode on suitable surfaces. The difference between these speed figures highlights a crucial aspect of real-world robotics: the balance between peak physical capability and the demands of safe, reliable, and often autonomous operation with a wheeled-legged robot. High speeds might be achievable under direct human control on ideal, open surfaces, but autonomous navigation in complex, cluttered environments typically necessitates slower, more deliberate movement to allow for sensor data processing, decision-making, and safety margins. Users should therefore base their expectations for autonomous tasks on the "operating max speed," while the higher figures indicate the robot's raw physical potential.
Beyond speed on the flat, the LYNX M20 can also tackle significant inclines, capable of ascending slopes up to 45 degrees. This capability is vital for operations in hilly terrain or on ramps within industrial facilities, showcasing its all-terrain robot credentials.
4.2. Conquering Challenges: LYNX M20 Stair Climbing and Obstacle Clearance
Navigating human-centric environments and unstructured terrain often involves dealing with stairs and various obstacles. The LYNX M20 is well-equipped for these challenges. It can climb continuous stairs with a step height of up to 25 cm (approximately 9.8 inches). This is a common stair height, allowing it to access many multi-level structures, a key feature for an adaptable industrial robot.
Even more impressively, the robot boasts a maximum single-step height (or obstacle clearance) of 80 cm (approximately 31.5 inches). This is a substantial capability for a robot that stands 57 cm tall. It means the LYNX M20 can overcome obstacles significantly taller than its own standing height, a feat likely achieved through its articulated legged mode and hyper-flexible joints. This dramatically enhances its utility in environments like disaster zones with large debris, active construction sites, or industrial facilities with high sills or unexpected obstructions. It significantly reduces the likelihood of the DEEP Robotics LYNX M20 becoming stuck or impeded, making it a more reliable asset for critical missions in hazardous environments.
4.3. Operational Stamina: LYNX M20 Battery Life in Demanding Scenarios
Endurance is a critical factor for any field-deployed robot. The LYNX M20 offers practical operational times. When carrying its effective payload of 15 kg, it has an endurance of 2.5 hours or a range of 12 km (approximately 7.45 miles). When unloaded, this extends to 3 hours of operation or a range of 15 km (approximately 9.3 miles). This ensures the industrial robot can complete lengthy tasks.
A single battery can be recharged in approximately 1.5 hours. These endurance figures are practical for many industrial shifts or specific mission durations. When combined with the 1.5-hour charge time and the hot-swappable battery feature discussed earlier, a small pool of just two or three batteries can enable the LYNX M20 to operate almost indefinitely. One battery can power the robot while another charges, allowing for a quick swap with minimal interruption. This operational model makes the LYNX M20 a true force multiplier, significantly reducing downtime compared to robots with fixed internal batteries that require the entire unit to be taken offline for lengthy recharging periods. This is a key design choice that maximizes its field utility and return on investment in industrial settings where operational uptime is paramount for robotic solutions.
5. LYNX M20 vs. LYNX M20 Pro: Understanding the Upgrades ⬆️
DEEP Robotics offers the LYNX M20 in two main variants: the standard LYNX M20 and the enhanced LYNX M20 Pro. While both share the same core physical platform and mobility capabilities, the Pro version comes with significant upgrades, primarily in computing power, autonomous functions, and connectivity. Understanding these differences is crucial for selecting the model that best aligns with specific operational needs for your industrial robot deployment.
The LYNX M20 Pro isn't just a minor specification increase; it represents a considerable leap in autonomous intelligence and system complexity. Key distinctions include:
- Computing Power: The standard M20 is equipped with dual octa-core 64-bit industrial processors (each with 16GB RAM + 128GB storage). The M20 Pro features three such octa-core processor units. This substantial increase in processing capability in the Pro model is likely dedicated to handling the more demanding algorithms required for its advanced autonomous navigation and SLAM (Simultaneous Localization and Mapping) functionalities.
- Autonomous Capabilities: While the standard M20 offers omnidirectional obstacle avoidance and point cloud surround view (with some aspects potentially enabled or enhanced via future OTA updates), the M20 Pro adds full SLAM-based positioning and mapping and autonomous navigation as standard, integral features. This means the Pro is designed for more independent and complex mission profiles, especially in unknown or dynamically changing environments where it needs to create its own maps and navigate without direct human guidance.
- External Interfaces: The standard M20 provides a 72V power input and a Gigabit Ethernet port. The M20 Pro expands on this by offering both 24V and 72V power input options, Gigabit Ethernet, and an additional USB 3.0 port. This gives the Pro version greater flexibility for integrating diverse payloads and peripheral devices, enhancing its role as a versatile wheeled-legged robot.
- Autonomous Charging: The capability for autonomous charging is listed as an optional feature specifically for the LYNX M20 Pro. This feature, when implemented with a compatible docking station, would enable true end-to-end autonomous missions for the Pro, including the ability to self-recharge and redeploy without human intervention.
These differences suggest that the M20 Pro is targeted at more advanced robotics users and applications demanding high levels of environmental understanding and minimal human oversight. The standard M20, on the other hand, might be more suitable for teleoperation or semi-autonomous tasks within more structured or pre-mapped environments when considering DEEP Robotics solutions.
6. Under the Hood: Detailed Technical Specifications of the LYNX M20 Series 📊
For those who need a granular look at the capabilities of the LYNX M20 and LYNX M20 Pro, the following table provides a side-by-side comparison of their key technical specifications. This information is primarily drawn from the official DEEP Robotics product pages, offering critical data for evaluating these industrial robots.
Table: LYNX M20 vs. LYNX M20 Pro Specifications
Feature | LYNX M20 | LYNX M20 Pro | Unit Conversion (Approx.) |
General Parameters | |||
Standing Dimensions (LxWxH) | 820 x 430 x 570 mm | 820 x 430 x 570 mm | 32.3 x 16.9 x 22.4 in |
Weight (incl. Battery) | 33 kg | 33 kg | 72.8 lbs |
Effective Payload Capacity | 15 kg | 15 kg | 33 lbs |
Max. Load Capacity | 50 kg | 50 kg | 110 lbs |
Unloaded Endurance / Range | 3 h / 15 km | 3 h / 15 km | 9.3 miles |
Loaded Endurance / Range (15kg) | 2.5 h / 12 km | 2.5 h / 12 km | 7.45 miles |
Charging Time (Single Battery) | 1.5 h | 1.5 h | |
Mobility Performance | |||
Lab-Tested Max. Speed | 5 m/s (safety-limited 3m/s user mode) | 5 m/s (safety-limited 3m/s user mode) | 18 km/h (11.2 mph) / 10.8 km/h (6.7 mph) |
Operating Max. Speed | 2 m/s | 2 m/s | 7.2 km/h (4.5 mph) |
Max. Continuous Stair Height | 25 cm | 25 cm | 9.8 in |
Max. Single-Step Height | 80 cm | 80 cm | 31.5 in |
Max. Slope | 45° | 45° | |
Hardware Configuration | |||
Computing Power | Dual octa-core 64-bit (16GB+128GB) x2 | Triple octa-core 64-bit (16GB+128GB) x3 | |
LiDAR | x2 (96-line, 360°x90° FOV, ~860k pts/s each) | x2 (96-line, 360°x90° FOV, ~860k pts/s each) | |
Wide-Angle Cameras | x2 | x2 | |
Environmental Adaptability | |||
Protection Rating | IP66 | IP66 | |
Operating Temperature | -20°C to 55°C | -20°C to 55°C | -4°F to 131°F |
Functional Features | |||
Omnidirectional Obstacle Avoidance | Yes (Future OTA for some aspects) | Yes (Future OTA for some aspects) | |
Point Cloud Surround View | Yes (Future OTA for some aspects) | Yes (Future OTA for some aspects) | |
Front/Rear Bidirectional Lighting | Yes | Yes | |
RF Image Transmission | Yes | Yes | |
OTA Upgrades | Yes | Yes | |
SLAM Positioning & Mapping | No (not standard) | Yes | |
Autonomous Navigation | No (not standard) | Yes | |
Autonomous Charging | Optional | Optional | |
External Interfaces | |||
Electrical Ports | 72V power input, Gigabit Ethernet | 24V/72V power input, Gigabit Ethernet, USB 3.0 |
This detailed, side-by-side comparison is invaluable for technically-minded individuals who need to scrutinize the exact capabilities of each model. It centralizes data from multiple official sources into an easily digestible format, clearly highlighting the Pro's enhancements in areas like autonomous navigation and computing power. The consistency in core mobility specifications (dimensions, weight, payload capacity, speed, endurance, etc.) between the M20 and M20 Pro, with the primary differences lying in computing hardware, autonomous software features, and interface options, strongly suggests a modular platform design from DEEP Robotics. The base chassis and locomotion system appear to be identical, with the Pro version receiving upgraded processing units and enhanced software licenses or capabilities. This modularity likely streamlines manufacturing and could potentially allow for field upgrades, though this is not explicitly stated. It means the fundamental physical performance and robustness are consistent across both models, and the choice between them hinges mainly on the desired level of onboard intelligence and operational autonomy for your wheeled-legged robot solution.
7. Unboxing the LYNX M20: What’s Included and Available Accessories? 📦
7.1. Standard Package Contents (Based on available information)
Pinpointing the exact contents of the standard LYNX M20 or M20 Pro package is challenging, as detailed official "what's in the box" lists are not readily available in most public domain research. This is quite common for specialized, high-value industrial equipment where configurations can be tailored to client needs. However, based on the robot's core features and typical inclusions for such advanced systems, buyers can likely expect:
- The LYNX M20 or LYNX M20 Pro robot unit itself.
- At least one hot-swappable battery pack, as this is a central design feature. The official specifications list "Charging Time (Single Battery)", implying one battery is standard.
- A compatible battery charger (logical for a battery-operated device with swappable batteries).
- A handheld remote controller is mentioned for the general DEEPRoboticsLynx model and is a common interface for such robots, though specific confirmation for the M20 series package is sparse.
- An operation manual and/or quick start guide (standard for complex equipment).
The general lack of a clearly itemized "what's in the box" list, even on detailed product pages, coupled with the "price on request" model, suggests that the LYNX M20 series is likely sold as a base platform. Components like extra batteries, specific control stations, or even initial software modules for this DEEP Robotics platform might be part of a customized quotation developed after consultation with DEEP Robotics or their distributors. This allows for tailored solutions but means potential buyers should anticipate a consultative sales process rather than a standard off-the-shelf purchase for this advanced wheeled-legged robot.
7.2. Expanding Capabilities: Official and Potential Accessories for the LYNX M20
The LYNX M20 series is designed for versatility, which is enhanced by its expansion capabilities, particularly its significant payload capacity. Known optional features and potential accessories include:
- An optional self-charging / autonomous charging station: This is specifically mentioned as an option for the LYNX M20 Pro, enabling truly independent, long-duration missions and enhancing its autonomous navigation capabilities.
- Modular Expansion: The robot is explicitly designed with "modular expansion capabilities" and features "a wide range of expansion ports and mounting interfaces". This inherent design philosophy is key to its role as an industrial platform. It encourages third-party development or custom in-house solutions for specific tasks, making the robot adaptable to a vast array of niche applications that DEEP Robotics might not cater to directly. This fosters an ecosystem approach rather than a closed, single-vendor solution for this all-terrain robot.
- While not officially listed, logical accessories would include additional battery packs to maximize uptime with the hot-swap system, and potentially various payload integration kits or specialized third-party sensors compatible with its mounting interfaces and data ports. Users should focus on professionally relevant expansions for this industrial robot.
8. In Control: Ease of Use, Software, and Maintenance of the LYNX M20 ⚙️
8.1. User-Friendly Operation: From Setup to Deployment of the LYNX M20
DEEP Robotics has designed the LYNX M20 with practical field deployment in mind. Its relatively lightweight design of 33 kg (72.8 lbs) means it can be transported and set up by a single operator. This significantly simplifies logistics compared to heavier robotic systems that might require specialized equipment or multiple personnel for deployment of an industrial robot.
Once in operation, features like omnidirectional obstacle avoidance and the robot's ability to autonomously adjust its posture and gait to varying terrains contribute to its ease of use. These intelligent functions reduce the cognitive load on the operator, allowing them to focus on the mission objectives rather than intricate piloting. While specific details on the M20's control interface are not abundant, general information for DEEPRobotics products mentions App support (likely for Android and iOS) and dedicated handheld remote controllers. Some online user comments have noted a "high level of raw handling", indicating responsiveness. The combination of single-operator portability and advanced autonomous functions aims to lower the barrier to entry for deploying sophisticated robotic solutions like the wheeled-legged robot LYNX M20 in challenging field conditions, potentially democratizing access to these capabilities for organizations that previously found them too complex or resource-intensive.
8.2. The Brains Behind the Brawn: LYNX M20 Software, OTA Updates, and Control Interfaces
The LYNX M20 series is powered by robust onboard computing. The standard M20 features dual octa-core 64-bit industrial processors (each with 16GB RAM + 128GB storage), while the M20 Pro is equipped with three such processor units. This processing power is essential for handling the complex AI algorithms, sensor fusion, and motion control that drive this advanced DEEP Robotics platform.
A key modern feature is support for OTA (Over-The-Air) software upgrades. This allows DEEP Robotics to deploy ongoing improvements, bug fixes, and even new functionalities remotely, ensuring the robot's capabilities can evolve and enhance over its lifespan. Notably, the official product information indicates that some key autonomous features, such as aspects of omnidirectional obstacle avoidance and point cloud surround view for the LYNX M20, are planned to be enabled or improved via "future OTA update". This software-defined platform approach means that early adopters might receive a robot with a foundational feature set, with the promise of significantly enhanced functionality over time without requiring hardware changes. This allows for quicker market entry for the hardware platform while the sophisticated software continues to mature. However, it also implies that buyers should clarify the current state and roadmap of these features at the time of purchase.
For remote monitoring and control, the system utilizes RF image transmission. As mentioned, control interfaces likely include mobile applications and dedicated handheld remotes, providing operators with the necessary tools to manage the robot during missions, including those involving autonomous navigation.
8.3. Keeping it Running: LYNX M20 Maintenance and Durability Insights
The LYNX M20's IP66 rating and generally robust build quality are designed to enhance its durability and potentially reduce maintenance requirements, especially when operating in harsh, dirty, or wet conditions. The hot-swappable battery system also simplifies one aspect of routine operation and helps maintain continuous uptime for this reliable industrial robot.
While no specific, detailed maintenance schedule for the LYNX M20 is provided in the readily available documentation, general best practices for field robotics would apply. User concerns noted in online forums about durability in specific extreme conditions, such as fine sand getting into joints of the all-terrain robot, are valid considerations for any mechanical system operating in such environments. The IP66 rating is designed to mitigate these issues, but regular inspection and cleaning, particularly of seals and moving parts, would likely be recommended to ensure long-term reliability.
The DEEP Robotics support website offers some basic troubleshooting tips for their robots (e.g., addressing motor overheat protection or controller connectivity issues) and outlines general warranty exclusions. These exclusions typically cover damage from misuse, unauthorized modifications, or exceeding safe operational limits. Interestingly, "Damage due to water, debris, or other chemicals getting inside the robot" is listed as an exclusion. While this might seem contradictory to an IP66 rating, it's common for warranties to have such clauses. An IP rating is a certification based on standardized tests under specific conditions and doesn't imply invulnerability to all forms of liquid or particulate ingress under all circumstances or durations of exposure (e.g., prolonged submersion or exposure to highly corrosive chemicals). Therefore, users must thoroughly understand the operational limits defined by the IP66 standard and adhere to recommended usage and cleaning guidelines to maintain the robot's integrity and warranty coverage when operating in hazardous environments.
9. Seamless Integration: LYNX M20 Compatibility and Developer Options 👨💻
9.1. Hardware Integration: LYNX M20 Ports and Payload Mounting
The LYNX M20 series is designed to be an adaptable platform, capable of carrying various payloads thanks to its impressive payload capacity. The standard M20 is equipped with a 72V power input and a Gigabit Ethernet port. The LYNX M20 Pro offers more versatility with 24V/72V power input options, a Gigabit Ethernet port, and an additional USB 3.0 port. These standard interfaces are crucial as they significantly simplify the integration of third-party sensors, manipulators, or auxiliary computing modules. Adherence to common industry standards like Gigabit Ethernet and USB 3.0 lowers the barrier for custom development, allowing users to leverage a wide ecosystem of existing compatible hardware without needing proprietary connectors or complex interface converters for this industrial robot. This can speed up development timelines and reduce integration costs.
The robot supports an effective payload of 15 kg (33 lbs) and is built with modular expansion capabilities, featuring various mounting interfaces to accommodate different equipment. While a specific, detailed payload integration guide or an exhaustive sensor compatibility list isn't provided in the general product literature for the DEEP Robotics LYNX M20, the availability of these standard ports and the stated payload capacity indicate a strong focus on enabling users to customize the robot for their specific applications.
9.2. Software and System Compatibility (Developer Options for LYNX M20)
For developers looking to create custom applications or integrate the LYNX M20 into larger robotic systems, understanding its software compatibility and development options is key. Specific Software Development Kit (SDK) or Application Programming Interface (API) documentation explicitly for the LYNX M20 series is not extensively detailed in the publicly available research reviewed.
However, DEEP Robotics maintains a GitHub presence (DeepRoboticsLab) where SDKs for other quadruped models, such as the Jueying Lite3 (Lite3_MotionSDK) and Jueying X30 (x30_motion_sdk), are available. These existing SDKs typically support popular programming languages like C++ and Python, and they provide functionalities such as accessing joint data, sending control commands, and interfacing via communication protocols including UDP, ROS (Robot Operating System), and CAN bus. It is plausible that similar SDK support would be available or is planned for the LYNX M20 series, particularly for industrial clients and research institutions, but direct confirmation is needed from DEEP Robotics. The LYNX M20's support for OTA upgrades further confirms its nature as a software-driven platform where capabilities like autonomous navigation can be managed and updated.
Prospective developers or integrators should directly consult DEEP Robotics for the most current and specific information regarding SDK availability, API documentation, and detailed communication protocols for the LYNX M20 and M20 Pro models, especially for developing advanced wheeled-legged robot applications.
10. Real-World Impact: Where the LYNX M20 Shines 🌍
The DEEP Robotics LYNX M20 series is not just a technological showcase; it's designed to deliver tangible benefits in a multitude of real-world scenarios, particularly those too dangerous, difficult, or inefficient for humans or conventional machinery. Its unique combination of wheeled speed, legged agility, robust environmental sealing (IP66 rating), and significant payload capacity makes it a versatile tool for industries ready to embrace advanced automation with this all-terrain robot.
Demonstration videos and company literature show the LYNX M20 confidently navigating rocky mountain trails, muddy wetlands, sandy deserts, debris-filled ruins, and even crossing unstable bridges and wading through shallow water. This ability to traverse such a wide array of challenging terrains is fundamental to its value proposition as a leading industrial robot.
Key application areas where the LYNX M20 is expected to make a significant impact include:
- Industrial Inspection: Performing routine or emergency inspections of power lines, pipelines, tunnels, mining sites, and large industrial plants. It can access confined spaces and hazardous environments, collecting data (e.g., visual, thermal, gas detection via mounted sensors) without risking human inspectors. The X30, a related DEEP Robotics model, is already being deployed for power cable tunnel inspections in Singapore, showcasing the practical application of this technology.
- Emergency Response & Public Safety: Assisting in disaster relief by navigating through rubble to locate survivors, assessing structural integrity of damaged buildings, or delivering emergency supplies. In firefighting, it could scout hazardous zones for temperature readings or chemical presence before human entry, demonstrating the value of robotic solutions in critical incidents.
- Logistics and Material Handling: Automating the delivery of tools, medical supplies, or samples across uneven or difficult terrain within large industrial complexes, construction sites, or even in outdoor environments with its wheeled-legged robot capabilities.
- Scientific and Environmental Research: Enabling data collection and exploration in remote or extreme environments that are challenging or costly to access by humans, such as geological surveys, wildlife monitoring in rugged areas, or environmental sampling.
- Construction and Surveying: Assisting with site surveying, progress monitoring, and carrying tools or materials in complex construction environments.
The LYNX M20's ability to operate in temperatures from -20°C to 55°C and its IP66 rating mean it can be deployed reliably in a wide range of climates and conditions, from freezing industrial sites to hot, dusty deserts, or during inclement weather, further broadening its applicability as a robust DEEP Robotics platform.
11. Weighing the Options: Pros and Cons of the LYNX M20 Series 👍👎
Based on available information and general characteristics of advanced robotics, here's a summary of potential pros and cons for the DEEP Robotics LYNX M20 series, a leading industrial robot:
11.1. Advantages:
- Unparalleled All-Terrain Mobility: The core strength is its hybrid wheeled-legged design, offering exceptional adaptability to diverse and extreme terrains where wheeled-only or legged-only robots might struggle.
- Robust Environmental Protection: IP66 rating and a wide operational temperature range (-20°C to 55°C) allow it to function reliably in harsh industrial and outdoor conditions, including hazardous environments.
- Enhanced Safety: Can undertake tasks in environments hazardous to humans, reducing risk to personnel in applications like inspecting unstable structures, handling dangerous materials, or scouting disaster zones.
- Operational Efficiency: Capable of autonomous operation (especially the Pro model with SLAM and autonomous navigation), potentially 24/7 with hot-swappable batteries, leading to increased productivity and reduced downtime.
- Versatile Payload Capacity: A 15 kg effective payload capacity allows for the integration of various sensors, tools, and equipment, making it adaptable to a wide range of tasks.
- Portability: At 33 kg, it can be deployed by a single operator, facilitating rapid deployment in various scenarios.
- Advanced Perception: Equipped with dual 96-line LiDARs and wide-angle cameras for comprehensive environmental awareness and navigation.
- Software Upgradability: OTA updates allow for future enhancements and new features, potentially increasing the robot's value and capabilities over time.
- Specific Pro Model Advantages: The LYNX M20 Pro offers superior computing power, dedicated SLAM and autonomous navigation, and additional interface options (USB 3.0) for more demanding autonomous missions.
11.2. Potential Considerations and Limitations:
- Complexity: As a highly advanced robotic system, it likely requires specialized knowledge for operation, maintenance, and particularly for any custom development or integration, despite efforts towards user-friendliness.
- Battery Dependence: While hot-swappable batteries significantly mitigate this, overall mission duration is still tied to battery life and the logistics of battery management (charging, swapping).
- Maintenance in Extreme Conditions: Despite the IP66 rating, prolonged operation in very abrasive environments (like heavy sand or corrosive atmospheres) may still necessitate diligent cleaning and maintenance of joints and seals to ensure long-term durability, a common concern for all-terrain robots.
- Software Maturity for Certain Features: Some advanced autonomous features are noted as being enabled or fully optimized via future OTA updates, meaning their current out-of-the-box performance might vary or be subject to an ongoing development roadmap.
- Cost: While pricing is excluded from this article per guidelines, advanced industrial robots of this caliber represent a significant investment.
- Limited Public Information on SDK/API for M20: Specific developer tools and documentation for the LYNX M20 series are not widely publicized, which could be a factor for teams planning extensive custom software development for these robotic solutions.
12. What Users Are Saying: Consumer and Community Feedback on the LYNX M20 🗣️
Direct consumer reviews for a specialized industrial robot like the LYNX M20 are not as common as for mass-market consumer electronics. However, reactions from tech communities, forums, and commentary on launch videos provide some early impressions of this DEEP Robotics innovation:
- General Amazement and Positive Reactions: Many online comments express awe at the robot's capabilities, particularly its agility and all-terrain performance. Phrases like "incredible robot," "this is great," and "amazing" are common in response to demonstration videos. The wheeled-legged design is often praised as a "really practical design".
- Impressive Mobility: Users have noted the "high level of raw handling" and are impressed by its ability to navigate varied terrains, including sand and water, and perform agile movements, essential for an all-terrain robot.
- Concerns about Durability and Maintenance: Some technically-minded observers have raised questions about long-term durability in harsh conditions, particularly regarding sand or fine debris affecting the joints, despite the IP66 rating. This reflects a practical concern for any field-deployed mechanical system.
- Battery Life Questions: Battery life and recharging logistics are common points of discussion, with users curious about operational endurance in real-world, demanding scenarios for this battery-powered industrial robot.
- Speculation on Applications (including non-industrial): As with many advanced robotic platforms, online discussions often include speculation about a wide range of applications, sometimes extending to security or even defense, though DEEP Robotics primarily markets the LYNX M20 for industrial use in areas like hazardous environments. Some users find the robot's appearance "a little creepy", while others compare its design to fictional robots.
- Desire for Real-World Usage Proof: Some commenters express a desire to see more evidence of these robots being used in actual, prolonged field deployments beyond promotional videos to fully assess their practical impact and reliability as advanced robotic solutions.
It's important to interpret this early feedback within context. Many comments are initial reactions to visual demonstrations rather than in-depth, hands-on reviews. However, they do highlight areas of public interest, excitement, and practical concern regarding the LYNX M20 series.
13. Looking Ahead: Sustainability and the Future of LYNX M20 ♻️
While DEEP Robotics has not published a specific, detailed corporate sustainability report or environmental policy for the LYNX M20 series itself in the provided research, the deployment of such industrial robots can contribute to broader sustainability goals in several ways:
- Reducing Human Risk and Improving Safety: By taking over tasks in hazardous environments, the LYNX M20 can prevent human exposure to dangers, contributing to social sustainability through worker well-being.
- Increasing Efficiency and Reducing Waste: In inspection tasks, robots like the LYNX M20 can provide more consistent and thorough data, potentially leading to earlier detection of faults or leaks in industrial processes, thereby preventing larger environmental incidents or material losses. Automated systems can often perform tasks with greater precision than manual methods, potentially reducing material waste in certain applications.
- Enabling Operations in Environmentally Sensitive Research: The robot's ability to navigate difficult all-terrain conditions could support environmental monitoring and research in sensitive ecosystems with potentially less direct human disturbance than traditional methods.
- Emergency Response: In disaster scenarios, faster and more effective response enabled by robots can mitigate environmental damage (e.g., containing spills after an industrial accident) and speed up recovery. DEEP Robotics has highlighted the use of their robots in emergency drills, specifically for scouting chemical explosion hazards and fire sites, where they gather crucial data on temperature, gases, and obstacles.
The LYNX M20 series, with its OTA update capabilities, is designed to be a future-proof platform. As AI algorithms improve and new sensor technologies become available, the robot's functionality can be enhanced, extending its operational life and adapting it to new challenges. The company's "AI+ Plan," which involves using new AI and software systems with extensive data for self-learning and training, aims to break the limitations of traditional models and achieve extreme motion capabilities, as well as extend to perception, planning, decision-making, and human-machine interaction with their wheeled-legged robots. This commitment to ongoing development suggests that the LYNX M20 will continue to evolve, potentially integrating more energy-efficient operational modes or components made from more sustainable materials as these technologies advance in the robotics industry.
14. Is the DEEP Robotics LYNX M20 Series Right for You? 🤔
The DEEP Robotics LYNX M20 series is undeniably a formidable leap forward in the realm of industrial-grade, all-terrain robotics. Its innovative wheeled-legged design, robust IP66-rated build, impressive obstacle negotiation, and significant payload capacity make it a compelling solution for a multitude of challenging applications where traditional robots or human intervention fall short. Whether you're looking to enhance safety in hazardous inspection tasks, improve efficiency in remote logistics, or pioneer new methods in scientific exploration, the LYNX M20 (and its more autonomous Pro sibling) offers a powerful and adaptable platform.
At BIKMAN TECH, we believe in empowering our readers with the knowledge to make informed decisions about cutting-edge technology. The LYNX M20 series is built for those who demand resilience, intelligence, and versatility in the most extreme environments. If you're ready to explore how this next-generation industrial robot can transform your operations, we encourage you to reach out to DEEP Robotics or their authorized distributors for a consultation and to discuss your specific needs for advanced robotic solutions.
Do you have questions about the LYNX M20, or experiences with similar robotic platforms? Share your thoughts in the comments below – we’d love to hear from you! And thank you for joining BIKMAN TECH for this in-depth look at the DEEP Robotics LYNX M20 series, a leader in autonomous navigation and all-terrain robotics.